Engineers devise a modular system to produce efficient, scalable aquabots
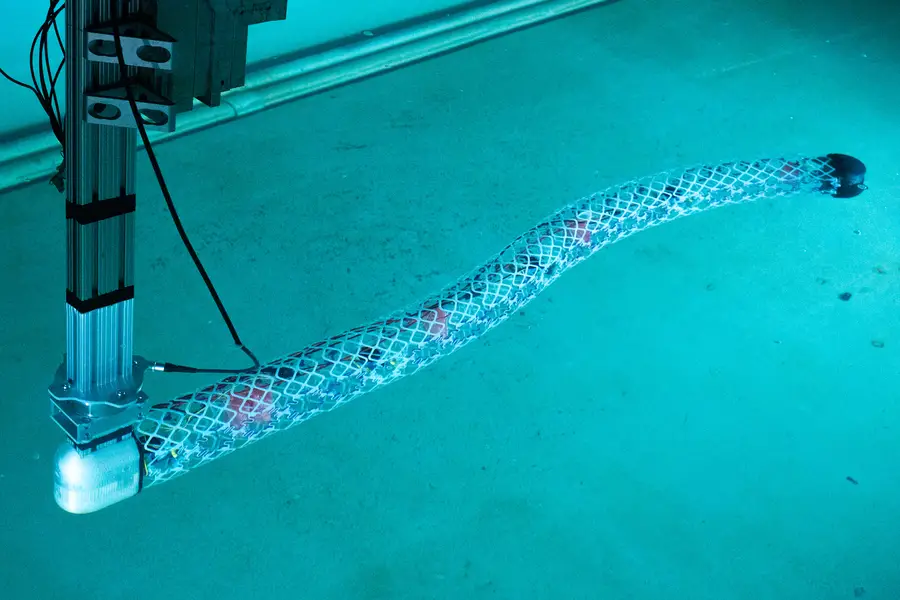
[ad_1]
The system’s easy repeating aspects can assemble into swimming varieties ranging from eel-like to wing-formed.
Underwater buildings that can alter their shapes dynamically, the way fish do, thrust via the h2o substantially a lot more effectively than conventional rigid hulls. But developing deformable equipment that can improve the curve of their physique designs although keeping a clean profile is a extensive and difficult method.
MIT’s RoboTuna, for illustration, was composed of about 3,000 diverse areas and took about two yrs to design and style and establish.

Scientists have occur up with an ground breaking solution to creating deformable underwater robots using simple repeating substructures. The workforce has demonstrated the new procedure in two unique illustration configurations, a single like an eel, pictured listed here in the MIT tow tank. Illustration by the researchers / MIT
Now, scientists at MIT and their colleagues — which include a person from the unique RoboTuna workforce — have developed an innovative technique to setting up deformable underwater robots, utilizing straightforward repeating substructures as an alternative of one of a kind components.
The group has demonstrated the new process in two unique example configurations, one like an eel and the other a wing-like hydrofoil. The scientists say the theory itself will allow for practically limitless versions in form and scale.
The function is remaining claimed in the journal Tender Robotics, in a paper by MIT research assistant Alfonso Parra Rubio, professors Michael Triantafyllou and Neil Gershenfeld, and 6 others.
Present methods to delicate robotics for maritime apps are usually manufactured on compact scales, even though a lot of handy serious-earth programs demand devices on scales of meters. The new modular system the scientists suggest could quickly be prolonged to this kind of measurements and further than, without having necessitating the form of retooling and redesign that would be necessary to scale up present systems.
“Scalability is a solid issue for us,” says Parra Rubio. Given the reduced density and significant stiffness of the lattice-like parts, known as voxels, that make up their process, he says, “we have much more home to retain scaling up,” whilst most presently used systems “rely on higher-density resources struggling with drastic problems” in relocating to greater measurements.
The unique voxels in the team’s experimental, proof-of-strategy devices are typically hollow structures made up of forged plastic parts with slender struts in complex styles. The box-like styles are load-bearing in 1 course but smooth in other individuals, an abnormal mix realized by mixing stiff and adaptable parts in distinct proportions.
“Treating tender versus difficult robotics is a wrong dichotomy,” Parra Rubio suggests. “This is a little something in concerning, a new way to assemble matters.” Gershenfeld, head of MIT’s Centre for Bits and Atoms, provides that “this is a 3rd way that marries the finest aspects of the two.”
“Smooth adaptability of the physique surface will allow us to implement circulation regulate that can lower drag and increase propulsive efficiency, resulting in considerable gasoline conserving,” claims Triantafyllou, who is the Henry L. and Grace Doherty Professor in Ocean Science and Engineering, and was portion of the RoboTuna crew.
In 1 of the units developed by the staff, the voxels are connected conclusion-to-stop in a extended row to variety a meter-lengthy, snake-like structure. The overall body is made up of 4 segments, each consisting of five voxels, with an actuator in the centre that can pull a wire attached to each of the two voxels on either facet, contracting them and leading to the framework to bend.
The whole structure of 20 units is then lined with a rib-like supporting framework, and then a restricted-fitting water-proof neoprene skin. The scientists deployed the construction in an MIT tow tank to clearly show its efficiency in the water, and shown that it was in fact capable of generating ahead thrust ample to propel by itself forward making use of undulating motions.
“There have been numerous snake-like robots just before,” Gershenfeld claims. “But they’re usually designed of bespoke elements, as opposed to these easy creating blocks that are scalable.”
For instance, Parra Rubio states, a snake-like robotic crafted by NASA was made up of hundreds of unique items, whilst for this group’s snake, “we demonstrate that there are some 60 pieces.” And when compared to the two many years expended creating and building the MIT RoboTuna, this system was assembled in about two times, he states.
The other gadget they demonstrated is a wing-like condition, or hydrofoil, produced up of an array of the similar voxels but equipped to change its profile shape and consequently manage the raise-to-drag ratio and other qualities of the wing. This kind of wing-like styles could be applied for a selection of reasons, ranging from producing electrical power from waves to supporting to strengthen the performance of ship hulls — a urgent need, as shipping is a considerable supply of carbon emissions.
The wing shape, in contrast to the snake, is included in an array of scale-like overlapping tiles, intended to press down on each and every other to retain a water-resistant seal even as the wing modifications its curvature.
One achievable software may possibly be in some type of addition to a ship’s hull profile that could lessen the development of drag-inducing eddies and so strengthen its overall performance, a risk that the group is discovering with collaborators in the delivery industry.
Scott Bergeron, running director for global engagement and sustainability at Oldendorff Carriers, states that “a range of innovative systems, like the MIT team’s demonstration of the feasibility of hydrodynamic morphing in cellular methods, symbolize promising adjustments to the classic layouts which can aid us satisfy the problem of the UN mandate to minimize the carbon footprint of shipping.”
Finally, the thought could be applied to a whale-like submersible craft, employing its morphable system form to build propulsion. This kind of a craft that could evade lousy weather conditions by keeping down below the area, but with out the sounds and turbulence of traditional propulsion.
The principle could also be utilized to parts of other vessels, these as racing yachts, wherever having a keel or a rudder that could curve gently all through a change instead of remaining straight could present an excess edge. “Instead of remaining rigid or just owning a flap, if you can in fact curve the way fish do, you can morph your way about the transform a lot extra efficiently,” Gershenfeld suggests.
Written by David L. Chandler
Source: Massachusetts Institute of Know-how
[ad_2]
Resource hyperlink