Unveiling the Versatility of Nickel Alloys: A Comprehensive Guide
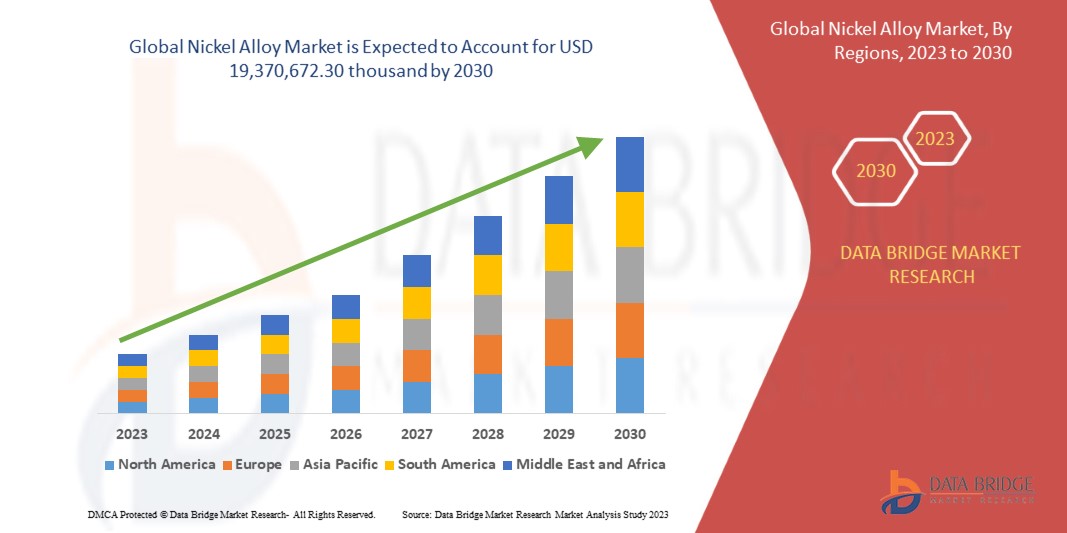
Nickel alloys, often referred to as superalloys, are a remarkable class of materials with an extensive range of applications across industries. Their exceptional properties, including high corrosion resistance, heat resistance, and strength, make them indispensable in various demanding environments. In this comprehensive guide, we will delve into the fascinating world of nickel alloys, exploring their composition, properties, and diverse applications. By the end, you’ll have a profound understanding of the role these alloys play in shaping the modern world.
What Are Nickel Alloys?
Nickel alloys are metallic materials that primarily consist of nickel along with other elements such as iron, chromium, and molybdenum. These alloys are engineered to exhibit specific characteristics that make them suitable for a wide array of applications. The key to their versatility lies in the precise control of alloying elements and manufacturing processes.
The composition of nickel alloys can vary significantly, resulting in various types tailored for specific requirements. Some common types of nickel alloys include Inconel, Monel, and Hastelloy. These alloys are known for their excellent resistance to corrosion, heat, and mechanical stress.
Properties of Nickel Alloys
Nickel alloys possess an impressive set of properties that make them valuable in numerous industries:
-
Corrosion Resistance: Nickel alloys are highly resistant to corrosion, particularly in aggressive environments, making them ideal for chemical processing and offshore applications.
-
Heat Resistance: These alloys maintain their structural integrity and mechanical properties at elevated temperatures, making them crucial in the aerospace and power generation sectors.
-
Strength and Toughness: Nickel alloys have a high strength-to-weight ratio and are known for their excellent toughness, crucial in applications subjected to mechanical stress.
-
Thermal Expansion: They exhibit a low coefficient of thermal expansion, ensuring stability in temperature-varying environments.
-
Electrical Conductivity: Some nickel alloys have good electrical conductivity, making them suitable for electrical components.
-
Magnetic Properties: Nickel alloys can be magnetic or non-magnetic, depending on their composition, offering versatility for different applications.
Applications of Nickel Alloys
The versatility of nickel alloys is evident in their wide range of applications across various industries:
-
Aerospace: In the aerospace industry, nickel alloys are used in engine components, airframe structures, and heat exchangers due to their exceptional heat and corrosion resistance.
-
Chemical Processing: These alloys play a vital role in chemical plants, where they resist the corrosive effects of acids, alkalis, and other harsh chemicals.
-
Power Generation: In power generation, nickel alloys are employed in gas turbines, nuclear power plants, and steam generators due to their ability to withstand high temperatures and stress.
-
Oil and Gas: The oil and gas industry relies on nickel alloys for equipment like valves, pumps, and tubing, which must endure extreme conditions in offshore drilling and refining.
-
Electronics: Certain nickel alloys are used in electronic components and connectors due to their electrical conductivity.
-
Marine: Nickel alloys are valuable in marine applications, where they combat the corrosive effects of saltwater.
-
Medical Devices: Some nickel alloys are biocompatible and find use in medical implants and surgical instruments.
Manufacturing and Fabrication of Nickel Alloys
The production of nickel alloys is a highly specialized process. It involves melting and casting the alloy, followed by various heat treatments to achieve the desired properties. The precise control of alloy composition and thermal processing is critical in ensuring the performance of the final material.
Nickel alloys can be fabricated into various forms, including sheets, plates, bars, tubes, and wire. Advanced machining techniques and welding methods are used to shape and assemble these materials into components that meet specific requirements.
Challenges and Future Developments
While nickel alloys offer exceptional performance, their production can be costly due to the high nickel content and the specialized manufacturing processes involved. As a result, researchers and engineers are continually exploring ways to optimize alloy compositions and production methods to reduce costs.
The future of nickel alloys is promising, with ongoing research into new compositions and processing techniques. This includes the development of high-entropy alloys, which are a class of materials containing multiple elements in roughly equal proportions, to achieve novel properties and enhanced performance.
To Know More Visit: https://www.databridgemarketresearch.com/reports/global-nickel-alloy-market
Conclusion
Nickel alloys have undoubtedly left an indelible mark on the world of materials science and engineering. Their exceptional properties have enabled innovation and advancement across industries, from aerospace and power generation to chemical processing and electronics.
As we look ahead, the quest for improved nickel alloy compositions and manufacturing methods continues, promising even greater versatility and applications for these remarkable materials. With their extraordinary resistance to corrosion and heat, strength, and adaptability, nickel alloys will remain a cornerstone in the construction of a more robust and resilient modern world.