IIT Jodhpur Develops Two step Approach For Textile Industry based Wastewater Recovery
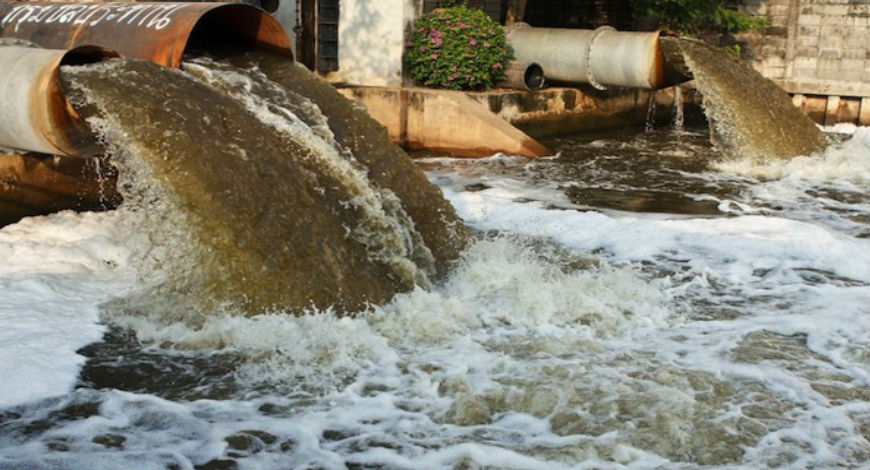
[ad_1]
Textile industries, as a single of the main consumers of water sources, make wastewater with intricate compositions, including toxic compounds, turbidity, significant colour and inorganic and natural compounds
Indian Institute of Engineering Jodhpur’s researchers has developed a two-move textile marketplace-dependent wastewater recovery strategy. The treatment contains the electrochemical processing of the sample in actual-time adopted by the authentic-time photocatalytic degradation applying novel ZnO caterpillars outgrown over carbon nanofibers in the next move. This technology possesses various rewards, decreasing the constraints of every approach when applied individually, alongside with the total degradation of pollutants, and no secondary pollution. The colored wastewater that emerged from textile industries can be processed with the explored technique and reused the treated drinking water for numerous other uses.
A vast selection of synthetic dyes produced by the textile marketplace endangers human and environmental health and fitness. Even trace quantities of synthetic dye in water are quickly noticeable and toxic to human overall health. Thus, there is a need to have for ground breaking cure procedures that can final result in the destruction of dye molecules in wastewater.
Dr Ankur Gupta, Assistant Professor, Section of Mechanical Engineering, IIT Jodhpur alongside with his exploration scholars Gulshan Verma and Prince Kumar Rai, and Prof. Jan Gerrit Korvink and Dr Monsur Islam from Karlsruhe Institute of Technologies, Germany, discovered out this two-move process for managing textile wastewater prior to discharging them into all-natural drinking water bodies.
The conclusions have been posted in Resources Science and Engineering Journal.
There is an escalating need to address the problem associated with contaminated water which is the consequence of a large quantity of metal and textile industries that launch a huge volume of polluted wastewater. Degradable organics, significant metals, dyes, surfactants, and pH-managed chemical substances are amid the contaminants uncovered in textile effluents (TEs). Textile industries, as a single of the big shoppers of water sources, generate wastewater with sophisticated compositions, like toxic compounds, turbidity, significant colour and inorganic and natural and organic compounds. In basic, the form and high-quality of TEs (reactive dyes) are utilized to create intricate wastewater with a higher chance of contamination and colouration. Most of the standard procedures (precipitation, ion exchange, membrane filtering, and so on.) are proving ineffective owing to the broad variation in the composition of textile wastewater. Therefore, there is a need to have for an alternate solution to triumph over this trouble.
The salient characteristics of the exploration are as follows:
– The integrated method presents higher organic subject removing efficiency with superior reduction of harsh colours current in true textile samples.
– Employing the vapour-liquid-stable method, a facile fabrication strategy is used to deliver ZnO caterpillars outgrown more than carbon nanofibers on Si substrate.
– Authentic-time textile wastewater degradation is monitored using the IoT approach by integrating a NodeMCU microcontroller board and a pH sensor.
The photo-catalytic decolourisation system will take ~240 min to rework the greenish-yellow textile effluent to colourless (~99.1 for every cent). Moreover, important quantities of TSS (~75 per cent) and TDS (~80 for every cent) were taken out from textile wastewater with the integration of electrochemical and photocatalytic degradation processes. Further, the hydrophobic nature (CA:130.35̊) of the fabricated ZnO caterpillars and electrochemical processing together has opened a new avenue for checking out and even more using for industrial wastewater procedure. As for each the researchers, the laboratory-centered proof-of-strategy can be scaled up to method industrial-released effluents and remediate wastewater.
[ad_2]
Supply website link India’s Indian Institute of Technology (IIT) Jodhpur has recently developed a two step approach for Textile Industry based wastewater recovery. This two step process was developed in order to reduce the amount of harmful chemicals and pollutants that get released into the environment due to the manufacturing process of textiles.
The first stage in this process involves the use of zeolites and ion exchange resins. These substances are known to absorb and trap chemicals and pollutants from wastewater before releasing them as harmless substances. The second stage of this process involves the use of a photocatalytic reactor, which helps in degrading and oxidizing toxins that are released from the wastewater.
This technology has been tested and studied extensively in multiple laboratories in India and it has been proven to be successful in recovering up to 90 percentage of waste textile effluent treated by this process. The results of the research have been published in the Journal of Environmental Chemical Engineering.
The two-step approach for wastewater recovery is a welcome change for the textile industry, which has long been known for its negative environmental impact. This technology can reduce the amount of hazardous compounds discharged from the manufacturing process and it can also protect the environment from further damage.
The research conducted by IIT Jodhpur will provide a solution to the problem of wastewater discharge from the textile industry. Not only does it have environmental advantages, but it also offers economic benefits as well. This technology can reduce the amount of money spent on wastewater treatment and it can also increase the efficiency of the manufacturing process.
IIT Jodhpur’s two-step approach for wastewater recovery is an important technological advancement in the textile industry. The research carried out by this organization will certainly have a positive effect on the environment and also result in economic savings in the long run. We hope that this technology will be adopted by other textile factories, so that the industry can become more efficient and the environment can be better safeguarded.